Maxfoam™
50-series

About 50-Series
The Maxfoam™ 50-series is a range of machines with a wide variety of options or retrofits available. You will find these machines all over the world producing a wide portfolio of flexible polyurethane foam for various industries. Examples include furniture, mattresses, automotive components, footwear, etc.
All models in the 50-series are based on the same modular design. This ensures flexibility and a machine that can benefit from a wide range of available options. It enables you to start with a low initial investment and rest assured that the machine can be upgraded and continue to grow together with your business, throughout the lifetime of the machine.
In true Laader Berg spirit the machines are designed for the operators ease of use, with full control through the powerful Maxfoam computer system (MCS™).

Maxfoam™ 5010
.

Our smallest foaming machine in the 50-series.
The design and small footprint of the Maxfoam™ 5010 makes it easy to design well working factory layouts, also where space is limited. Additive tanks can be positioned either on the left or right side of the foaming tunnel, and with its four section fall plate and 14-meter-long foaming tunnel it can produce a wide range of products.
Based on the robust Maxfoam principle, trough and fall plate, the machine is easy to master and will quickly be turning valuable raw materials into premium polyurethane foam.
Maxfoam™ 5020
.

Probably the most sold Maxfoam machine in the world.
The design and medium sized footprint of the Maxfoam™ 5020 makes it easy to design well working factory layouts, also where space is limited. Additive tanks can be positioned either on the left or right side of the foaming tunnel, and with its five section fall plate and 20-meter-long foaming tunnel it can produce a wide range of products.
Based on the robust Maxfoam principle, trough and fall plate, the machine is easy to master and will quickly be turning valuable raw materials into premium polyurethane foam.
Maxfoam™ 5025
.

A ramped-up version of the 5020, with standard equipment like conveyorized sidewalls, Pintomax™ flat top system, hanging mixer, traversing Liquid Lay-Down system and high output pumps as standard.
The design and footprint of the Maxfoam™ 5025 makes it easy to design well working factory layouts for high throughput setups. Additive tanks can be positioned either on the left or right side of the foaming tunnel, and with its six section fallplate and 22-meter-long foaming tunnel, it can produce a wide range of products.
Based on the robust Maxfoam principle, trough and fallplate, the machine is easy to master and will quickly be turning valuable raw materials into premium polyurethane foam.
With the included hanging mixer and traversing Liquid Lay-Down system the machine is also prepared for technical foam types or foaming with high reactivity formulations.
The Pintomax™ system will work together with the Maxfoam system and further increase foam yield by optimizing the squareness of the foam block.
(prepared for 3-step mixing)
Maxfoam™ 5035
.

Top of the 50-series range.
Based on the Maxfoam™ 5025, but further optimized for maximum productivity. With our longest available foaming tunnel with conveyorized sidewalls, 3-step mixing, spacious working platforms and very high output pumps as standard.
Based on the robust Maxfoam principle, trough and fall plate, the machine is easy to master and will quickly be turning valuable raw materials into premium polyurethane foam.
The 3-step mixing system of the Maxfoam™ 5035 includes the silicone mixer, which is standard for the 50-series, combined with a floor pre-mixer and a hanging final mixer.
The Pintomax™ system will work together with the Maxfoam system and further increase foam yield by optimizing the squareness of the foam block.
With the included 3-step mixing system and traversing Liquid Lay-Down system the machine is also prepared for technical foam types or foaming with high reactivity formulations.
Contacts
Laader Berg has a global presence with representatives in every corner of the world, providing top-notch services to customers worldwide
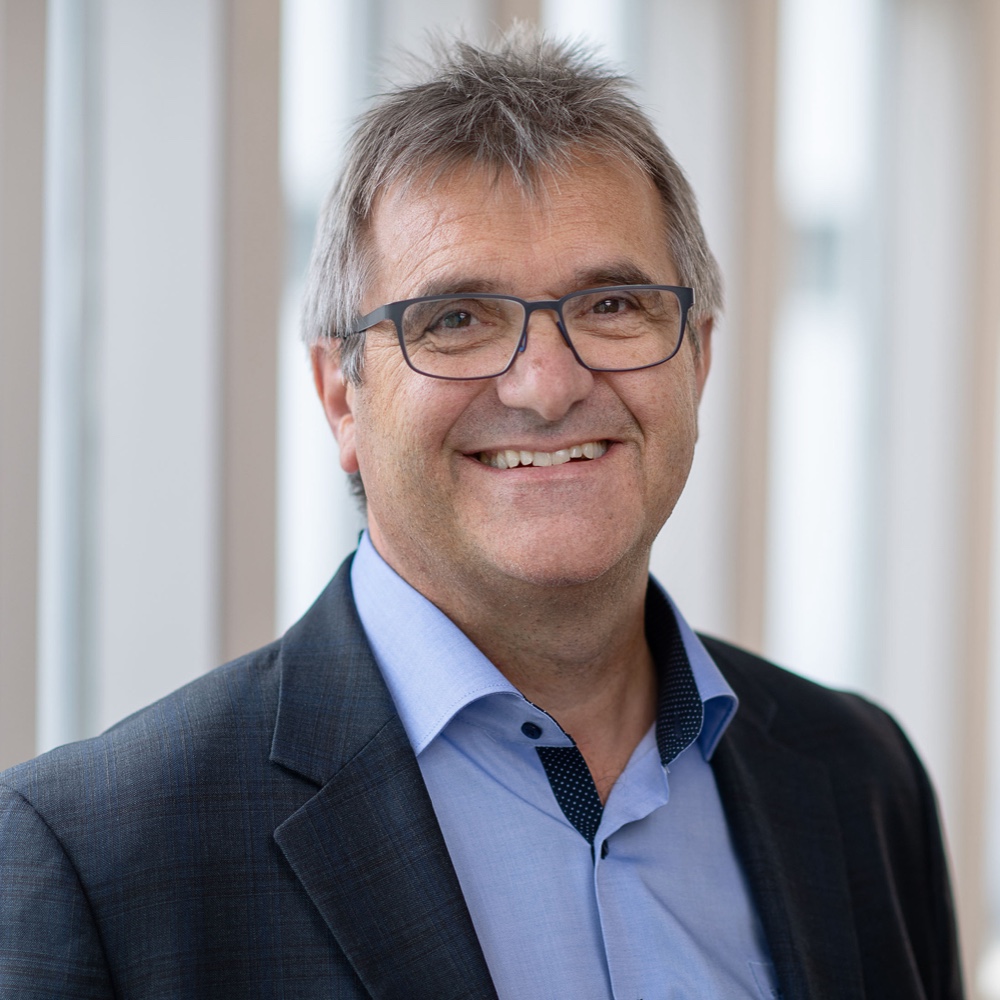
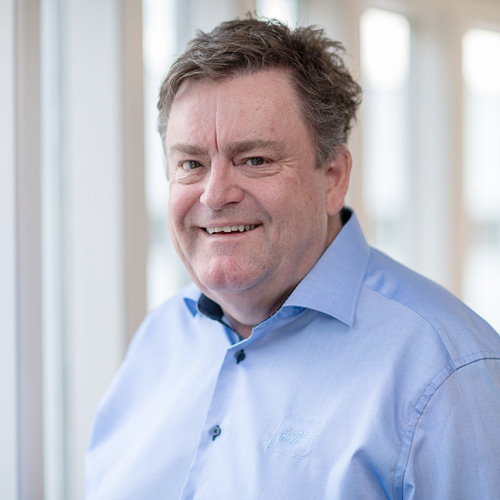
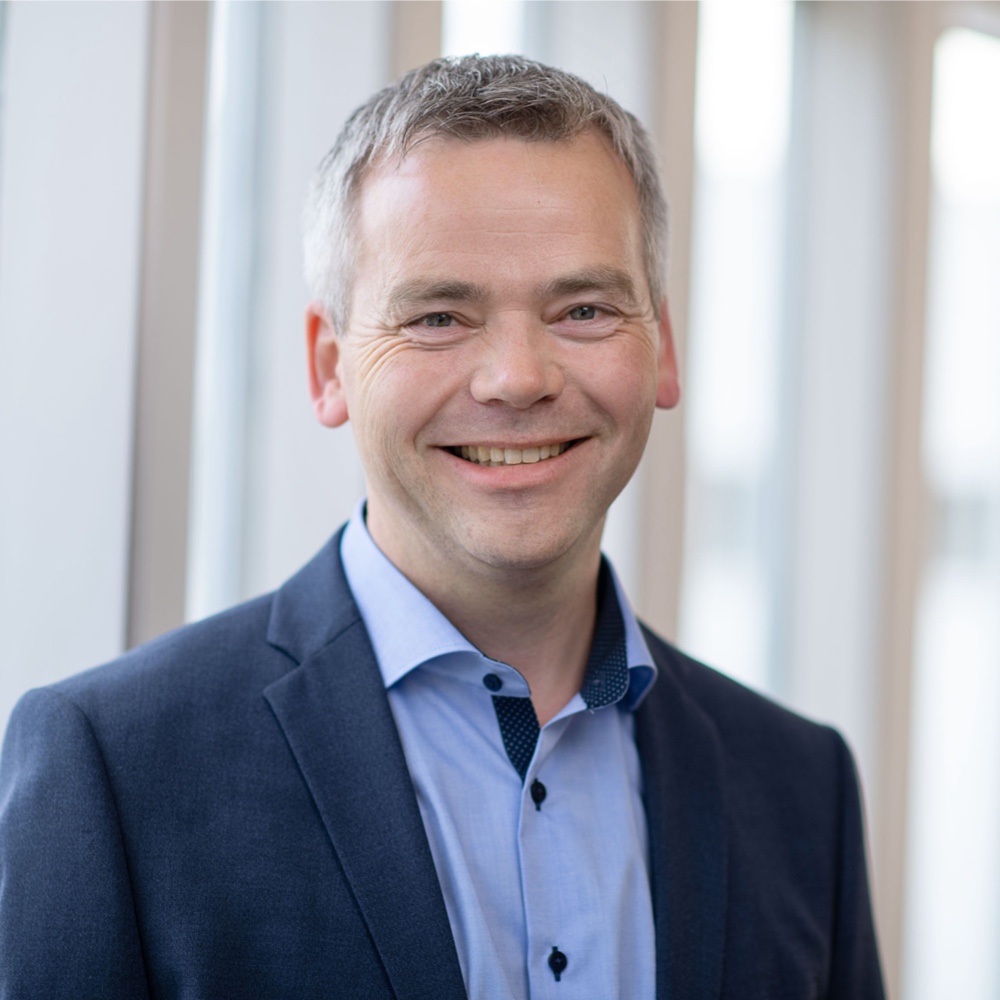